How to Make a Good Mesh
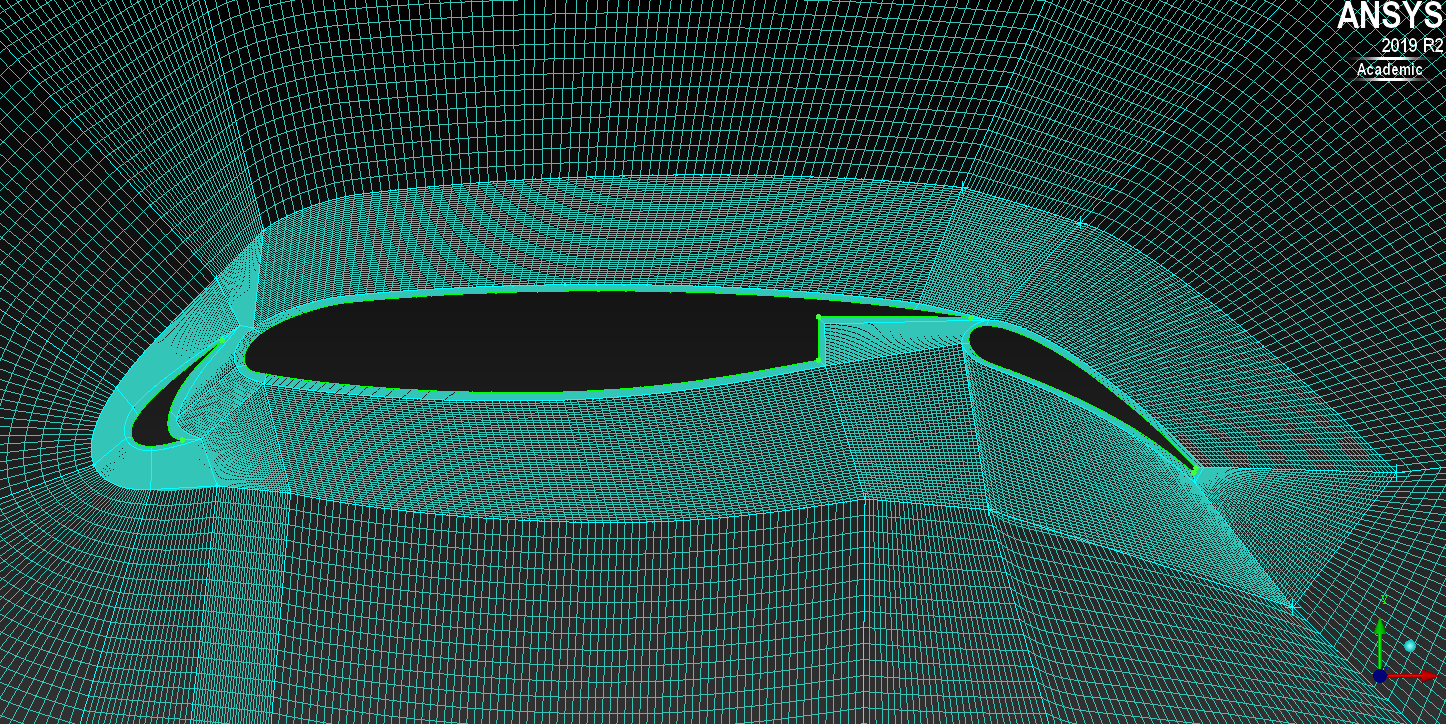
Making a good mesh is an important aspect of CFD analysis as the quality of the mesh affects the accuracy and reliability of the simulation results. Here are some general tips for making a good mesh:
- Consider the geometry of the problem: The mesh should accurately represent the geometry of the problem being analysed. This includes ensuring that the mesh is sufficiently refined in regions where the flow is expected to change rapidly.
- Choose an appropriate mesh type: There are different types of meshes, such as structured, unstructured, and hybrid meshes. The choice of mesh type depends on the complexity of the problem, the desired level of accuracy and the computatinal resources available.
- Use appropriate element shapes: The elements of the mesh should be chosen based on the geometry of the problem and the physics being studied. For example, triangular elements may be more suitable for modeling fluid flows with complex geometries, while hexahedral elements may be more suitable for modeling fluid flows in regular geometries.
- Refine the mesh: The mesh should be refined in regions where the flow is expected to change rapidly, such as boundary layers, shocks, and wakes. The level of refinement should be chosen based on the desired level of accuracy.
- Perform a mesh convergance study: This analysis determines the level of mesh refinement required to achieve a desired level of accuracy in the simulation results. The study involves systematically varying the mesh size and observing how the solution changes as a function of the mesh size. The idea is to refine the mesh until the solution becomes independent of the mesh size, indicating that the simulation has converged to a solution.
- Check for mesh quality: The quality of the mesh should be checked to ensure that the elements are not distorted, and the aspect ratios are not too large. Mesh quality can be improved by adjusting the mesh density and element shape.
- Use adaptive mesh refinement: Adaptive mesh refinement is a technique that automatically refines the mesh based on the flow characteristics. This can improve the accuracy of the simulation while minimizing computational resources.
In summary, making a good mesh involves selecting an appropriate mesh type, refining the mesh in critical regions, using appropriate element shapes, performing mesh convergance study, checking for mesh quality, and using adaptive mesh refinement when appropriate.
How to Check the Quality of a Mesh
The quality of a mesh affects the accuracy and convergence of the numerical solution, thus it is important that the mesh has sufficiant quality. Here are some common metrics used to measure the quality of a mesh:
- Aspect Ratio: Aspect ratio is a measure of the ratio of the length of the longest edge of an element to the length of the shortest edge. A high aspect ratio indicates a mesh element is highly distorted, which can cause numerical inaccuracies in the solution.
- Skewness: Skewness measures the deviation of an element from a perfectly orthogonal or regular shape. High skewness can cause numerical errors, particularly for simulations involving turbulence modeling.
- Orthogonality: Orthogonality measures the angle between the faces of an element. High orthogonality is important for accurate simulation of flow near solid surfaces.
- Smoothness: Smoothness measures the continuity of the mesh across adjacent elements. A smooth mesh ensures better accuracy of the numerical solution.
- Mesh Density: Mesh density is a measure of the number of mesh elements per unit volume. A higher density is required in regions where the flow field changes rapidly, such as near solid surfaces, shocks or boundary layers.
- Aspect Ratio and Skewness Histograms: Histograms of aspect ratio and skewness values can provide a quick overview of the distribution of the mesh quality, and help identify regions with poor mesh quality.
There are various software tools available for measuring mesh quality, which calculate these metrics and provide visualizations of the mesh quality. It is important to ensure that the mesh quality meets the required standards for the particular application of the CFD simulation.
What areas need more attention than others
Areas of a mesh that need more refinement are those where the flow field changes rapidly, such as near solid surfaces, shocks, or boundary layers. These areas are typically characterized by high gradients in flow properties such as velocity, pressure, and temperature.
Near solid surfaces, the mesh needs to be refined to capture the flow physics accurately, particularly in the boundary layer region where the velocity gradients are high. The boundary layer region is important as it affects drag and thus the overall performance of the device.
In the case of shocks, the mesh needs to be refined in the region immediately upstream and downstream of the shock. The shock is a discontinuity in the flow properties, and hence a finer mesh is required to accurately capture the shock location and intensity.
Additionally, regions where there are complex flow features such as vortices, wakes, and jets may also require a higher mesh density. These regions are often characterized by rapidly changing flow directions and strong gradients in flow properties.
In general, it is important to ensure that the mesh is refined in regions of interest to accurately capture the flow physics. However, a balance between mesh refinement and computational cost needs to be maintained, as overly refined meshes can lead to excessively long simulation times.