Introduction to Computational Fluid Dynamics
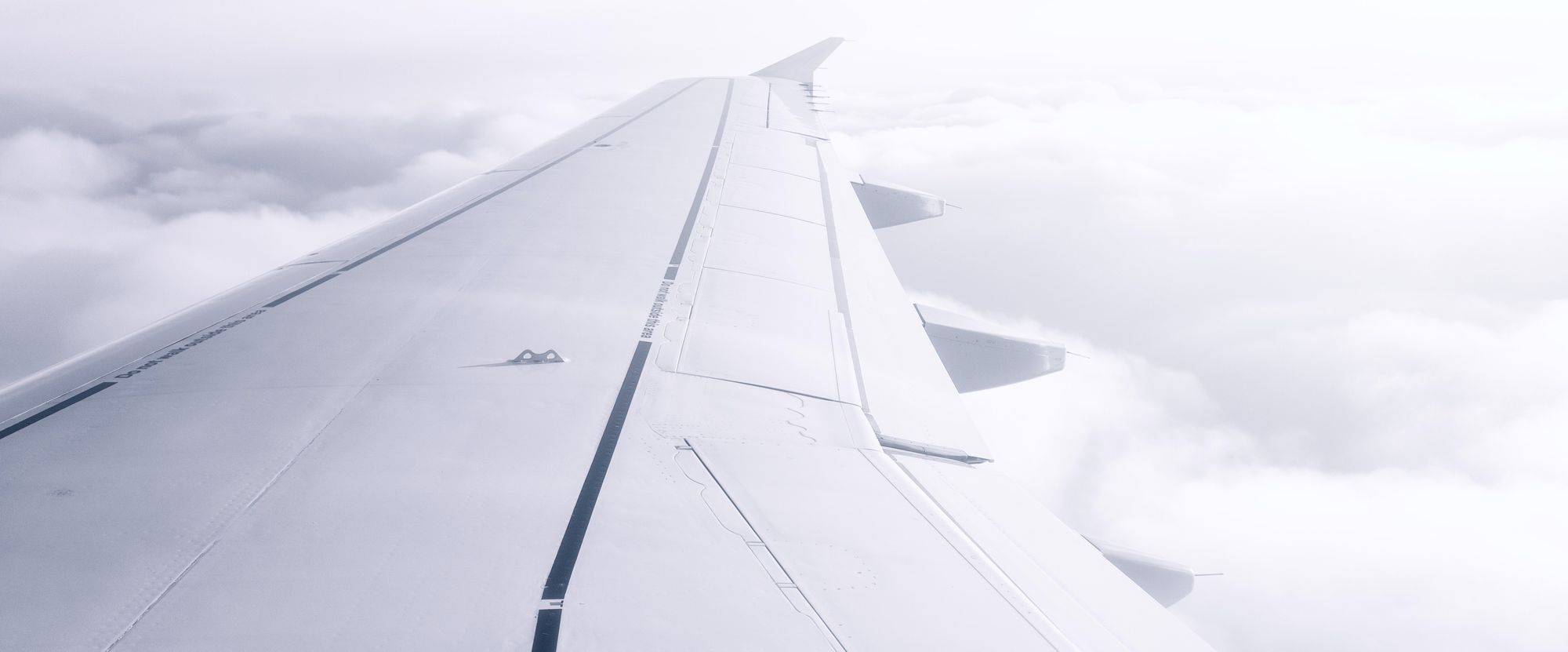
What is Computational Fluid Dynamics?
Computational Fluid Dynamics (CFD) is a numerical simulation technique used to analyse and predict the behaviour of fluid flows. The method involves solving complex mathematical equations that describe the physical phenomena of fluid flow, heat transfer, and chemical reactions
CFD can be used to simulate a wide range of fluid flows, including laminar and turbulent flows, compressible and incompressible flows, as well as multiphase flows. The simulations can provide information on a range of fluid properties such as velocities, pressures, temperatures, and others, which can then be used to analyse and optimise the performance of various systems and devices. Many industries use CFD, for example in aerospace, automotive, energy, and biomedical engineering which use CFD to design and optimise various products and systems, such as aircraft wings, wind turbines, combustion engines, and medical devices.
CFD is typically used in engineering design to optimize the performance of products and systems. For example, it can be used to:
- Design more efficient aircraft wings or engine components to reduce fuel consumption and emissions.
- Optimize the performance of heat exchangers or cooling systems in electronics to prevent overheating.
- Analyze the flow of fluids in chemical reactors or mixing tanks to optimize the production process and ensure product quality.
- Simulate the flow of air or water in buildings or urban environments to optimize ventilation and reduce the risk of pollution or contamination.
The basic steps in CFD analysis are as follows:
- Pre-processing: first a digital model of the system or environment being analysed is created, with defined boundaries and initial conditions of the fluid flow, and selecting appropriate numerical methods and algorithms.
- Numerical solution: The mathematical equations that describe the fluid flow are solved using numerical methods such as finite element analysis or finite volume method. These equations are solved for each time step to track the fluid flow and its behavior.
- Post-processing: Once the numerical solution is obtained, post-processing is performed to analyze the results and visualize the fluid flow and its behavior. This includes generating plots, graphs, and animations to represent the results in a meaningful way.
Advantages of CFD:
- Allows for the study of complex fluid flow phenomena that are difficult or impossible to observe in experiments.
- Can be used to study a wide range of fluid flow problems, including both internal and external flows.
- CFD simulations can provide detailed information about flow quantities, such as velocity, pressure, and temperature, which can be difficult to measure experimentally.
- CFD can help engineers optimize designs for improved performance and efficiency. Can help reduce development costs and time by allowing some design optimisation before prototyping and testing.
Disadvantages of CFD:
- CFD simulations can require a high level of expertise and computational resources to set up and run.
- Simulations are sensitive to the quality of the input data, such as the mesh and boundary conditions, and can produce inaccurate results if not set up correctly.
- CFD results are only as accurate as the underlying models and assumptions used, which can lead to errors and uncertainties in the results.
- Simulations can be computationally expensive and time-consuming, particularly for large and complex problems.
- CFD simulations can be limited by the available computing resources, which can restrict the size and complexity of the problems that can be solved.
Therefore, CFD can be used when physical experimentation or testing is not feasible, too expensive, or too time-consuming. It can also be used in conjunction with experimental data and engineering judgment to make informed design decisions by providing additional insights and information.
When using CFD, it is important to ensure that the simulation is validated against experimental data or theoretical predictions. The accuracy of the results depends on the quality of the input data, the numerical methods used, and the assumptions made in the simulation. It is also important to understand the limitations of the simulation and to use it in conjunction with other methods to ensure that the results are reliable and meaningful.